Heading out the door? Read this article on the new Outside+ app available now on iOS devices for members! Download the app.
This article was originally published in 2017, when Fred worked with Adidas/FiveTen. Though he no longer works at the brand he continues to design shoes, now for SoILL!.
Fred Nicole has been an important figure in bouldering since the 1990s. In 1996, he established the world’s first V14, Radja, and then in 2000, the first V15: Dreamtime. In 2016, at age 46, Nicole put up Chakijana, a V14/15 boulder problem in Rocklands, South Africa. Though he’s stepped out of the climbing spotlight in recent years and has always been a reclusive, enigmatic figure—a soft-spoken “man of the forest”—he’ll have something new to offer the community in fall 2017: climbing shoes.
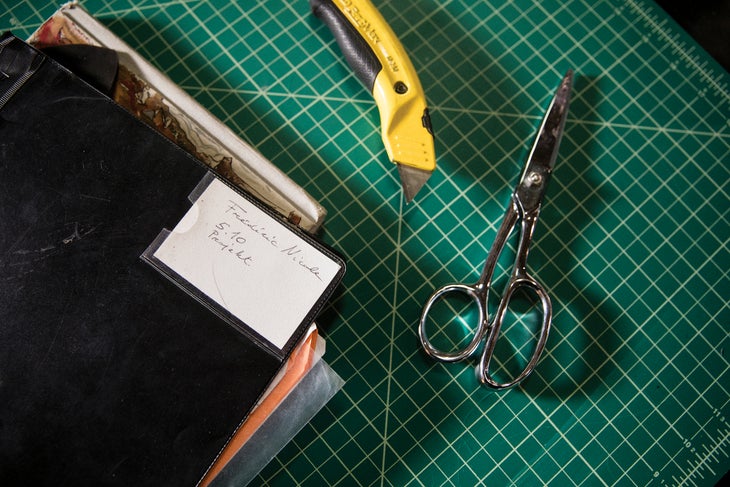
More than 15 years ago, Nicole began working at Gecko Supply GmbH in Zurich, Switzerland, resoling climbing shoes. Here, he began tinkering with his own shoes, looking for ways to improve them, taking apart the original Five Ten Anasazi Velcro and rebuilding the shoe on his own last. Now, he gets to design his shoes from top to bottom. It’s been an interesting transition: While only Nicole’s personal investment in a boulder problem is at stake with each attempt, a rock shoe will make an impression on thousands of people.
“For me and a boulder problem, it will just be a personal feeling,” Nicole says. “But when you make a climbing shoe, it will be mainly about what others think.”
Living in Zurich, where he’s been for 20-plus years, Nicole does most of his work at Gecko Supply. He talks frequently with designers at Five Ten via Skype, email, and phone, and also travels to Five Ten’s HQ in Redlands, California. Throughout, Nicole has applied the traits that have defined his bouldering career—vision, creativity, refinement, and perseverance.
Vision
Walking through the woods of Cresciano, Switzlerland, in early 2000, Nicole found what would become Dreamtime. It was on a hillside in an area he hadn’t climbed at before. On a 30-degree overhang, crimps and clean-cut slopers swooped out steel-blue stone. At first, the moves felt improbable, but piece-by-piece they began to come together.
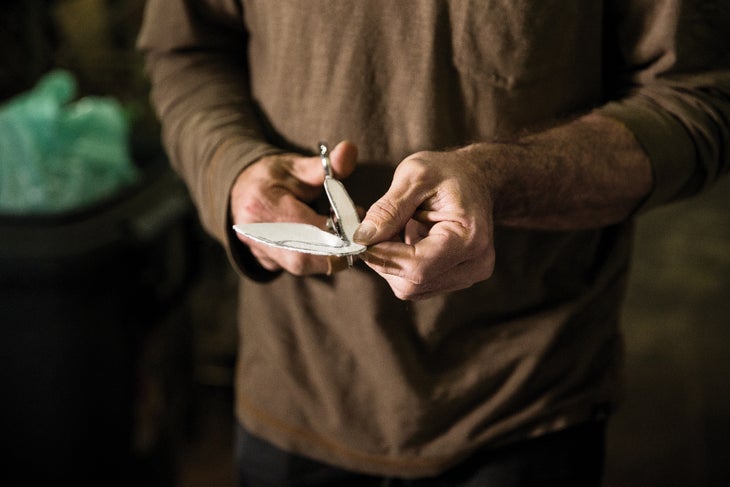
For Nicole, designing a shoe is the personal process of figuring out how to create a seamless union of climber and rock. With his project for Five Ten, he will likely be designing multiple models.
“I’m not specifically making one type of shoe, because I don’t like the same shoe for every type of climbing,” he said. “Even if I like sensitive shoes, I would like to be able to design an edging shoe that still has that sensitivity. There should be a good interaction between you and the shoe. That’s the point, I guess: to have something working and reacting well with your body.”
Nicole has approached shoe design with the same openness with which he first approaches a boulder problem. After several short trips out to the boulder, Dreamtime was “like a sketch drawing,” he says. He could do some of the moves and had a vague idea of the line, but it would still take many days of effort to tease out the details. “It was hard to read and understand how to use the handholds at first,” he says. “You have to be creative to be able to interpret the rock, and translate it to movement.”
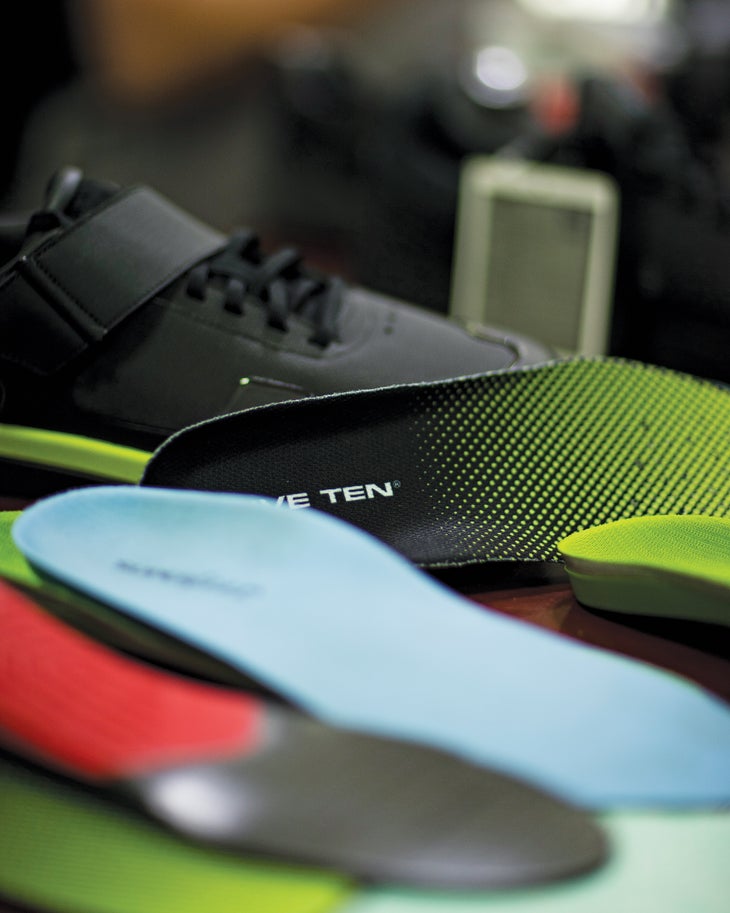
Similarly, piecing together a prototype from an idea for the “perfect shoe” isn’t easy. “I know how a shoe should ideally react, but it’s not always easy to transfer what is more like a feeling to an actual shoe,” says Nicole.
Creativity
Dreamtime didn’t strike Nicole as an incredible problem because of any one move. Instead, “the aesthetic of the line is what struck me,” he says. Though it became a new standard for bouldering, he didn’t climb it for the sheer difficulty. “The rock itself is something unique. I did it for the purity of the line,” he says.
In the small room of a three-story brick building in Zurich, home to Gecko Supply, Nicole wears a mask to protect against the fumes from sanding rubber and strong glues. Though the room gets plenty of natural light from the single-pane windows, each piece of machinery has its own overhead light so Nicole can scrutinize the details. Industrial belt sanders create the workshop’s heavy feel, while shelves lined with skin-colored foot models (lasts) sit below pictures of his past ascents and travels. Scraps of rubber cover the floor—for a single shoe model, he might cut five different types of rubber. Sketches and notes from past attempts help him adjust his working model.
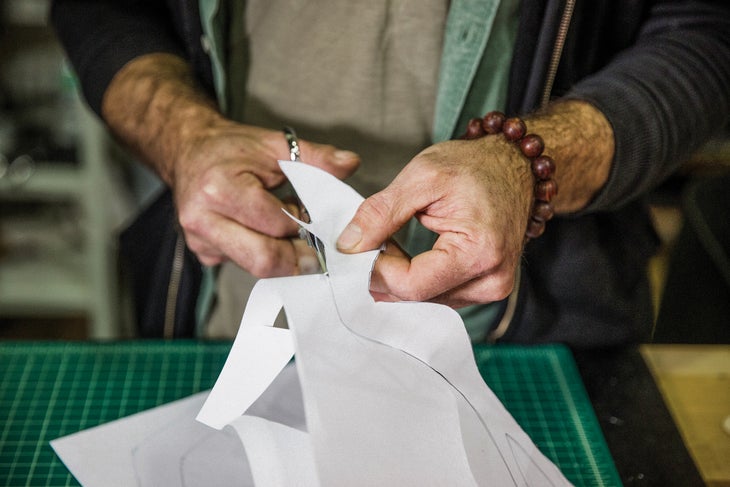
Nicole has been sponsored by Five Ten since 1994. He remembers quite a few “favorite shoes” he’d love to climb in again, but he doesn’t want to rehash old classics. “It would be great to find a new way to get that same kind of performance,” he says.
As you create a new rock shoe, you face dozens of options at every turn, each of which can have a profound effect on overall fit and feel. Just changing the rand rubber can change the tension you feel when toeing onto an edge, even though no part of the rand makes contact with the rock. Similarly, making a soft midsole will allow you to use the tension throughout the shoe to toe-hook, whereas a stiffer midsole will benefit edging performance.
On one recent model, Nicole experimented by adding extra rubber to the arch for support. At first, he started with a softer rubber made for a more sensitive shoe, but once the shoe had set over several days, he found that it no longer held tension. And so, it was back to the drawing board.
Today, just over six months into the design process, “I feel more comfortable with the creative part of designing, but I’m slowly learning to be more methodical and precise,” Nicole says. “It’s an empirical method, where you test and adjust until it works.”
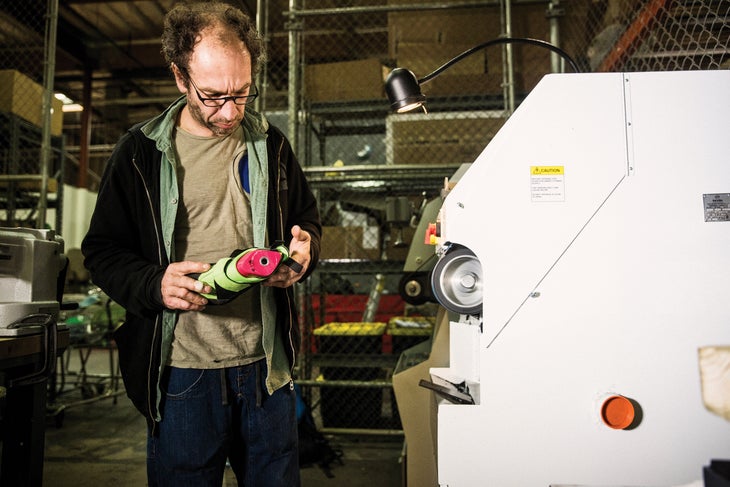
To track his progress, Nicole keeps a detailed notebook to record all the tiny changes and adjustments he’s made to each model. Prior to a shoe’s final prototype, when it’s ready for testing, Nicole will compile 20 or more pages of drawings and notes.
Refinement
While working Dreamtime, Nicole surprised himself by figuring out the basic movements over a handful of sessions. But, after that, the details became important. The tiny crimps and slopers didn’t give way unless each move was done just right—late into his first season on Dreamtime, he fell close to a dozen times on the final moves. Subtle changes to the starting beta—picking the exact location for each foothold and making micro-adjustments in body position—were the only way to avoid falling at the end.
A rock shoe comes together when the designer has picked a last, the material for the upper, the midsole, the sole, and the rand rubber (see “8 Steps to a New Rock Shoe”). Each aspect has an important effect on the overall feel, but that integral effect might not be obvious until the shoe is assembled and tested.
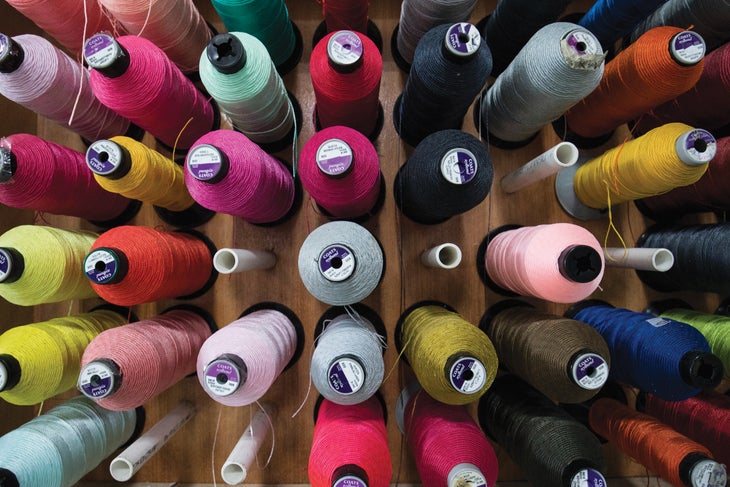
“Once the shoe is built and randed, you do tests with your colleagues and make changes until a few are happy with it. Then, we can start to share them with sponsored climbers to test and get their feedback,” Nicole says.
For the past two years, Nicole has been working closely with Five Ten as a tester. He’s learned firsthand how this process works. If a shoe passes muster, it might continue toward production with only a few tweaks, or it could face a complete overhaul and retesting. Now that Nicole’s on the other side of the fence, he’s found that not everything is as easy as he’d like: “That first feeling is generally not what the shoe will be in the end,” Nicole says.
Though he can’t talk details on models in production, Nicole is anticipating the first tests on one of his designs. “I am quite happy with what I have right now. It’s something that really fits my foot, but we will have to see with others,” he says. Nicole has been testing with fellow Swiss climbers on the Alps’ limestone, granite, and sandstone. “I try to use them on different terrain, all types of features and types of rock,” Nicole says. But, as he’s said, it can be hard to translate that impression into a better shoe. Couple that with different feet and it becomes more challenging—it isn’t just a matter of making a shoe stiff or sensitive, or downturned or flat, but tailoring the overall fit and tension so that the shoe will work in a similar fashion for many different climbers.
Perseverance
Nicole traveled to South Africa and Australia after his first season on Dreamtime, which made coming back to it in autumn 2000 more difficult. Some days it was just about showing up and trying, even if the holds felt slick with October’s warmth. Though he was into his second season now and approaching 20 days of effort, sending wasn’t his only goal; he also wanted to enjoy the process—even if that meant failing on the last moves repeatedly. “It can be even more frustrating to focus on the end goal,” he said. “I tried my best on each attempt, but I was not always thinking about the send.” As November brought cooler temps, Nicole topped out the block.
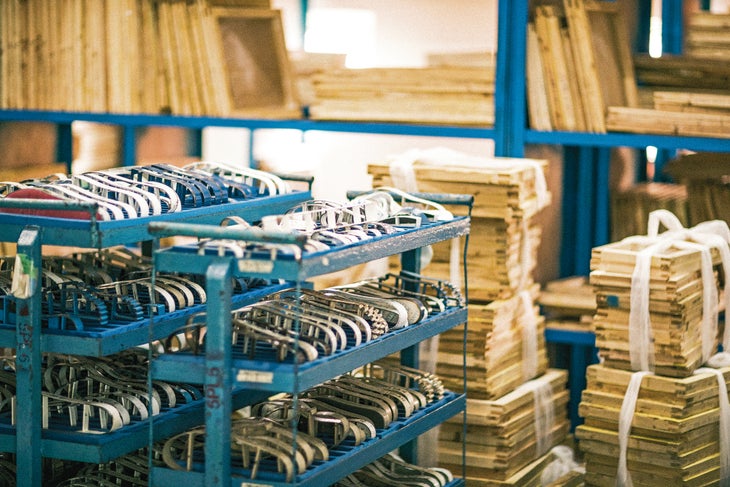
While it’s easy to look back on his ascent of Dreamtime, Nicole is reluctant to sum up his experience with Five Ten just yet. “Right now, we are really in the process … so it’s hard to talk about it,” he says. “The climbing shoe is living its own story.”
As for the factors within his control, Nicole has one lesson he’s been able to apply directly from climbing: “It is one of my mistakes in climbing,” he says. “Generally, when I do find a way to do a move, I often stick with it. Many things I’ve done have been done later with better beta, and now I’m a little more aware of that.” A prime example might be Radja: Other climbers later found a different—almost separate—line not tried by Nicole that dropped the grade to V13. With shoe design, Nicole is trying not to develop tunnel vision.
“It’s especially tough when you imagine something being really great and it doesn’t turn out that way at all. Being able to question yourself over and over is the key,” he says. “I am learning, which is good.”
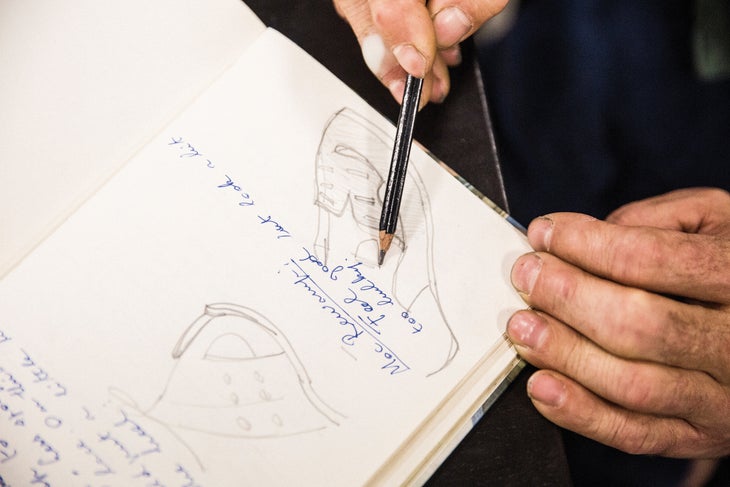
Much as Nicole has patiently spent days and sometimes months learning the nuances of the world’s hardest boulder problems, he has now happily immersed himself in a design apprenticeship. “I like it and it’s an interesting process, and it’s a new direction in my life as well,” says Nicole. “Before, I was just kind of wearing a shoe, but now I am looking at how to make and test a new shoe to see what is really good or not.”
8 Steps to a New Rock Shoe
Before we start, a few key terms:
Last: The unique, foot-shaped mold around which the shoe will be built.
Sole: Where the rubber meets the rock—the shoe-bottom rubber you climb on.
Midsole: This interior sole brings the shoe together; different materials and variations will change overall feel.
Footbed: The fabric your foot will be in contact with.
Upper: The socklike upper portion of the shoe, often made of leather or a synthetic material.
Rand: The thin layer of rubber that covers the bottom and sides of the shoe.
1. There are two ways to build a last:
- Board-lasting: The shoe designer will take a “board,” the stiff toe-to-heel shape of the shoe bottom, and attach it to the footbed. The upper is then fit around the last and attached to the footbed and board, creating a stiff shoe from end to end.
- Slip-lasting: Slip-lasted shoes begin by first attaching the footbed to the upper, then slipping the combined footbed and upper over the last. Resembling a sock with an extra-thick bottom, slip-lasted shoes have very little structure until the midsole is attached. Because of this, they are much more versatile, and are used in most modern shoe designs.
2. Designers pick which material they’ll build the shoe with: leather or synthetic. Leather shoes will stretch, often up to half a size, whereas synthetics tend to hold their shape better.
3. Designers attach the midsole, giving the shoe its shape as well as determining its intended usage. Using a stiff, firmly attached midsole will yield a rigid, edging-type shoe, while a softer midsole makes for a more sensitive shoe that can also smear, heel-hook, toe-hook, and grab edges.
4. Next, warm rand rubber is fit around the base of the shoe. This thin layer covers the shoe bottom and sides. The sole attaches to this.
5. The thicker sole rubber is glued over the rand, which is still visible around the heel and toe box, though many brands will add additional rubber to fortify certain high-traffic sites.
6. Specialized machinery presses the final, glued shoe to make sure each part seals firmly into the next.
7. After the shoe has had a few days to dry, the sole is hand-machined to have crisp edges and a polished look.
8. The shoe is distributed to the testing team for feedback. From there, there may be further revisions based on that feedback or even a complete reimagining before market.