Industrial Boomtowns Rise In Unlikely Places As Labor Shortages Shift Site Selection
Rail has always been the economic backbone of Dillon. Throughout the 20th century, trains shipped tobacco and cotton from this South Carolina town to processing plants up and down arteries on the Eastern Seaboard. By the 1990s, the tobacco industry was in sharp decline, and the trains to and from Dillon slowed to a crawl.
Nearly 30 years later, trains are active once more, hauling cargo containers 160 miles from Charleston — one of the South’s busiest ports — into a new $50M distribution hub called Inland Port Dillon.
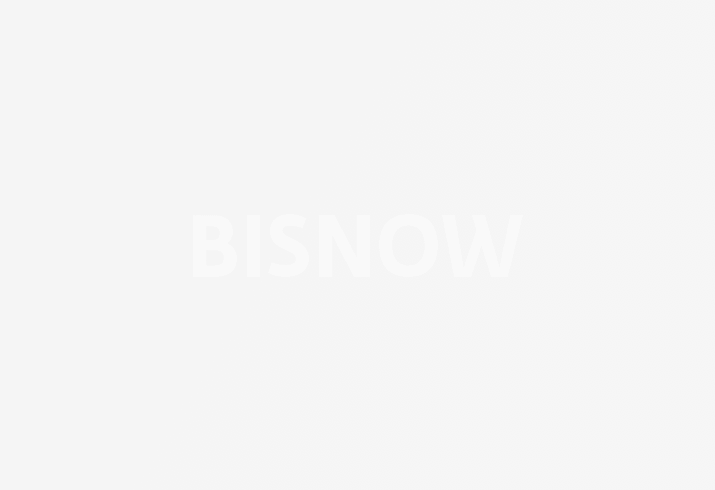
Once a forgotten town in the heart of the Deep South, Dillon, with a population of 6,604, is now overtaking cities more than 40 times its size to become an anchor of America’s burgeoning warehouse and e-commerce fulfillment center explosion — a $24B construction surge that is being brought into the U.S. mainstream.
Dillon is reaping those dollars, but it is far from alone.
From Fremont, Nebraska, to Locust Grove, Georgia, to Front Royal, Virginia — all communities with populations less than 30,000 — the next industrial boomtowns are springing up in seemingly unexpected places across rural America. These distribution hubs are attracting newfound population and myriad development opportunities that never would have been possible in the last decade.
The End Of Tradition
The drive to rural America is spurred by a lack of available land in traditional industrial centers like Chicago and Indianapolis, along with the latest advances in technology that are allowing distribution companies to move further from central hubs. And rural communities have begun to exploit their advantages: plentiful land, a low cost of living, access to major highways and an abundance of affordable housing.
Though labor can be an issue in some of these areas, automation is now being used to bridge the gaps. The rise of automation is broadening where distribution companies can locate to send their goods to the masses, which is making more expensive urban logistics less appealing, CBRE Global Head of Industrial & Logistics Research David Egan said.
Additional advancements, such as same-day delivery, are also pushing companies to locate closer to consumers in rural areas that have the same service demands as metro populations, he said.
At Inland Port Dillon, it has all been about getting products to consumers faster.
In addition to a plentiful workforce of about 390,000 within 30 miles of the site, Inland Port Dillon touts its location on Interstate 95 — which runs through almost every major population center on the East Coast, from Boston and New York City to Miami — as a competitive advantage for logistics companies. Port Dillon is expected to reach a capacity of 40,000 containers by the end of the year, which puts it on par with some of the largest ports in the U.S.
The New Industrial Boomtowns
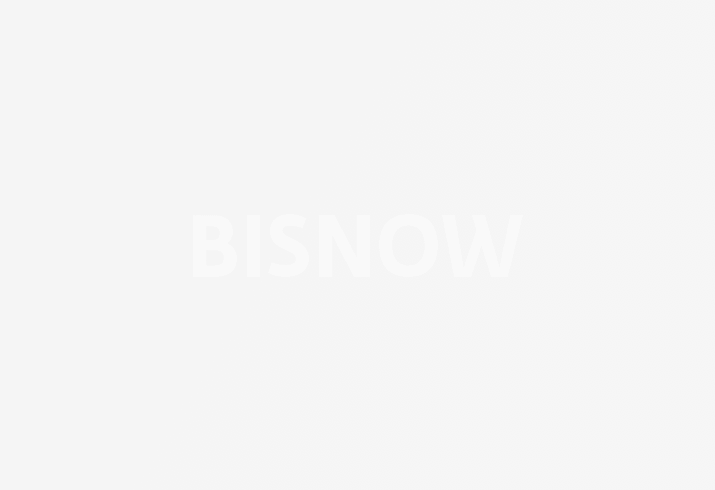
What is transpiring at Inland Port Dillon has already happened at Front Royal, Virginia, an inland port 300 miles from the Port of Richmond. Opened in 1989, the port led to more industrial, retail and residential development in the surrounding area because the labor demanded it, CBRE Research Manager Brian Reed said.
“Like Dillon, [Front Royal] was built in the middle of nowhere and there wasn’t much of a population,” Reed said. “It provides a long-term vision for what Dillon might become. [Front Royal] has had a significant amount of investment.”
Front Royal’s population has grown 38% since 1990. Industrial volume has increased in recent years, and the Virginia Port Authority had the highest rail volume of any port system on the East Coast as of 2017. It set a new record in 2016 for handling over 2.6 million 20-foot containers. The port also led to a $500M, 1M SF Procter & Gamble plant at Tabler Station, West Virginia, about 45 minutes away. The agency is considering further expansion of its inland port system to bring more economic activity to far-away places in Virginia, activity that goes beyond warehouses and shipping.
“While [Front Royal] development was mostly industrial, there was a labor component and the area ended up with more retail and more residential just because the labor demanded it,” Reed said.
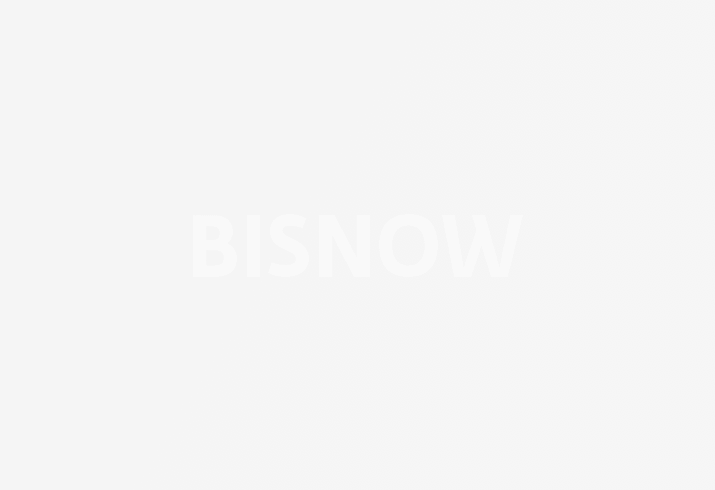
Other rural areas throughout the South and Midwest are receiving similar attention. CBRE Senior Vice President Trey Pennington said the Southeast has been a base for manufacturing for generations, and the next wave, this time of large distribution centers, is starting to hit.
South Carolina is a good case study. Inland Port Dillon is hoping to mirror the success of another South Carolina inland port, Port Greer, which is near the hub of Greenville/Spartanburg, population 68,000. Port Dillon is not near a major metro, showing the move deeper into rural areas.
“The growth of distribution in the Greenville/Spartanburg market is largely spurred by development of the Inland Port Greer,” Reed said. “It’s all about getting goods into the country as fast as possible.”
Inland Port Greer opened in 2013, 200 miles from the Port of Charleston. It has been so productive that the South Carolina Ports Authority reached its container volume five-year goal of 100,000 units in two years, SCPA Director of Strategic Projects Micah Mallace said.
“We had no idea that was going to happen,” he said.
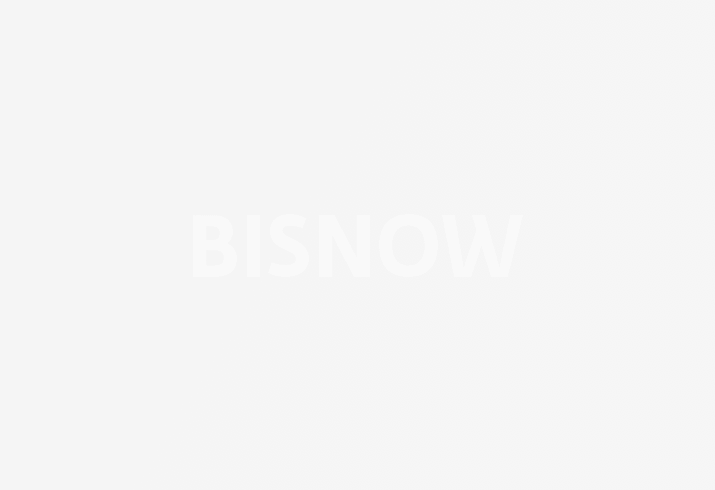
Five years into its life, Greer already has major investments from big-city names: BMW, Michelin, Adidas, Eastman Chemical Co., Dollar Tree and Rite-Aid. This has led to tremendous growth in the greater Greenville/Spartanburg industrial market. Occupied warehouse square footage grew 25% to over 67M SF and manufacturing square footage grew about 24% to over 87M SF from 2009 to 2017, according to data collected by CBRE.
Greenville/Spartanburg’s multifamily market has been on the rise since Port Greer opened in 2013, with developers delivering 4,700 units in the last 24 months, according to data from Marcus & Millichap.
“This is a great example of exactly how the inland port can bring development to an area that wouldn’t otherwise get it,” Mallace said. “We’re seeing companies, not just developers, locate [at Port Greer] and Dollar Tree is a great example. Part of Dollar Tree’s thought process was an inland port would dramatically reduce transportation costs. That’s a huge plus in our corner to decide to locate there.”
The Growing Pains of Boomtowns
Building in some rural and suburban locations, especially if there isn’t a qualified workforce, could be tempting fate. If a community has only 20,000 people, and facilities need 5,000 employees, it gets tough to fill the jobs. And even if there isn’t a lack of labor, there is often a lack of necessary skills, Reed said.
Luckily, many workers are willing to commute long distances to these jobs. The Lehigh Valley Economic Development Corp. CEO Don Cunningham has certainly seen this.
The Lehigh Valley — an area straddling Pennsylvania and the western edge of New Jersey — is one of the country’s hottest industrial markets, with more than 110M SF of warehouse space as of 2017 and another 5M SF of spec warehouse space coming this year. Operators of these facilities are pulling employees from a more than 45-mile radius around the Lehigh Valley.
Many of those employees commute into the Lehigh Valley from as far away as the Philadelphia suburbs and the Pocono Mountains area, a one-hour drive. Logistics employment has jumped from 18,000 people five years ago to just shy of 30,000 today, Cunningham said.
“So far, we haven't seen any kind of crisis in it,” he said. “But the question remains: How much can we grow at this pace?”
Those distances may be a bigger deal for warehouse workers, who are often filling positions at minimum wage.
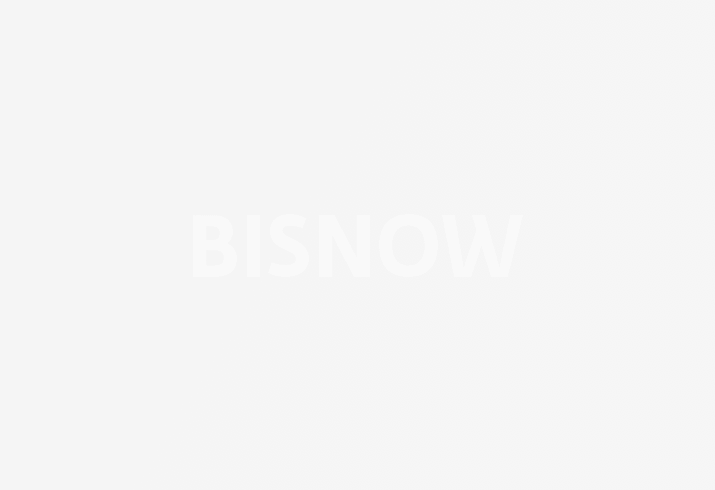
“It's pulled some minimum wage workers out of other arenas, like bricks-and-mortar retail, landscaping, whatever it might be where people were working for minimum wage or a little bit above minimum wage,” Cunningham said.
Attracting people to come to work in Lehigh Valley has emerged as a bigger part of his organization’s job, including working with local universities, colleges and even high schools, as well as reaching out to neighboring communities to ensure that logistical firms will have enough potential hires.
“Across the country, community colleges and technical schools are addressing new labor requirements with training programs tailored for specific skill sets,” Biggins Lacy Shapiro Project Director Industrial & Supply Chain Practice Leader Michelle Comerford said.
“The question for us is how deep can that go? How many workers are on the bench still who aren't participating in the labor market for one reason or another? We don't know the final answer but we're very involved in the process of trying to stimulate that,” Cunningham said.
Even with that outreach, Cunningham said it is only a matter of about five years before that labor pool may be topped out.
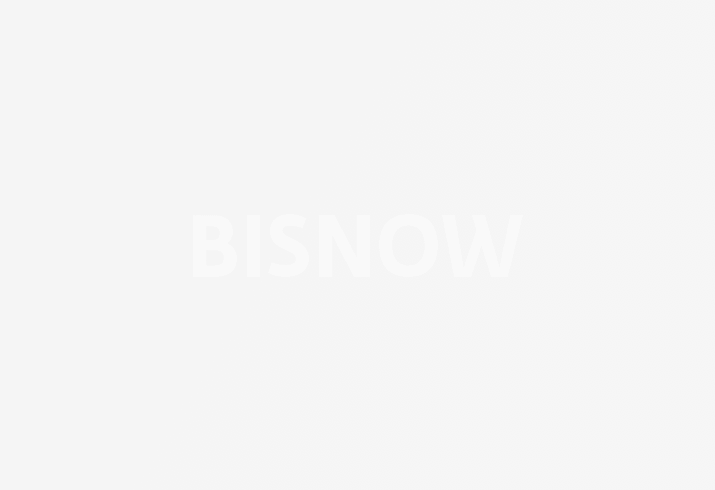
The next wave of this solution is attracting employees to move to these rural areas, and that requires amenities and housing. People moving to rural areas from bigger cities to fill logistics jobs expect a similar lifestyle, Egan said. Garry Clark is experiencing that in Fremont, Nebraska. Clark is the executive director of the Greater Fremont Development Council as well as a board member of the National Rural Economic Development Association.
Discount membership retailer Costco is underway with a chicken plant in the community that is expected to spur 800 new jobs, a big jump for a community of 20,000, Clark said.
The city conducted a study that concluded that the area’s current housing stock falls short of what will be needed for an influx of workers for Costco and companies in industries the retailer will attract to the region. The city expects to need upward of 900 additional residential units — a mix of single-family to multifamily — to house these workers, Clark said.
To help encourage development, the city — with help from state funding — is starting a workforce housing fund to help finance private projects that will create new housing units in the city. That program is expected to launch this month.
“There’s been a lot of development in Fremont prior to Costco, but I think it definitely propelled the Fremont, Dodge County area to another level,” Clark said. “This is a national issue right now as far as workforce housing in rural places and also the workforce itself.”
Bring In The Robots
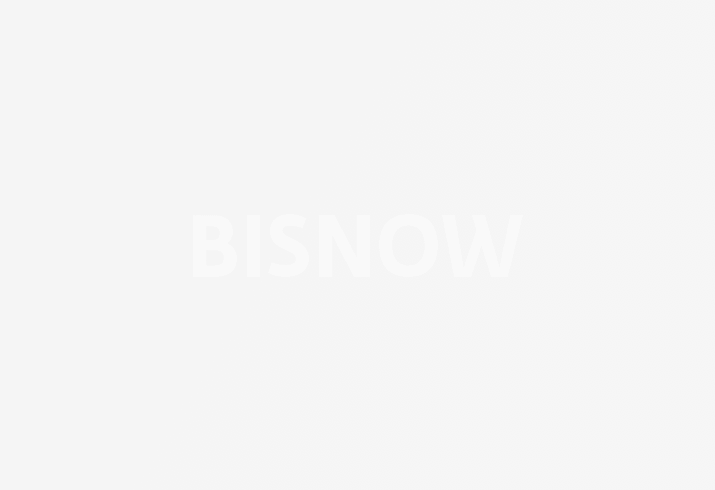
Automation can fill the labor gap — robots are increasingly playing a role in distribution centers, and the shift to self-driving cars could be a major factor in pushing logistics activity to rural areas — but that puts further strain on the required skill set for human laborers, and some fear one day automation could go too far and replace jobs in these tiny towns.
Robots are already overtaking some small-town populations, with a heavy concentration in manufacturing operations. The Midwest and South are starting to have more robots per capita. Morristown, Tennessee, has 16.6 robots per 1,000 workers, while Kokomo, Indiana, has 35.2 robots per 1,000 workers, according to a report from The Brookings Institution. There are 35 small metro areas with five or more robots per 1,000 workers. Comparatively, Detroit, which has 15,000 industrial robots, has 8.5 robots per 1,000 workers.
As of 2015, there were 233,305 industrial robots, most of which were welding, painting cars, assembling products and packaging items in 10 states. Michigan has 12% of the nation’s total robots with Ohio, Indiana and Tennessee rounding out the top four.
“A lot of [companies] are starting to plan for a day that they're going to start to use more robotics,” Pattillo Industrial Real Estate CEO Larry Callahan said. “We're starting to see it and it's something to start thinking about.”
Sure a warehouse operation could drop from, say 1,000 employees to just a few hundred thanks to automation. But people will still need to be there, Callahan said.
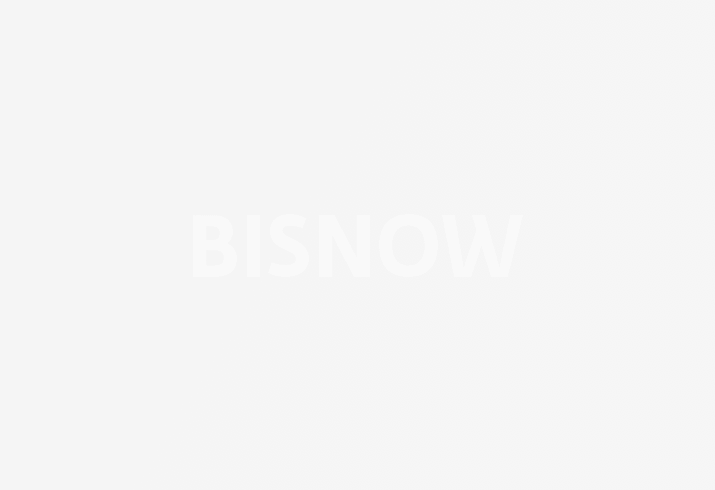
Self-driving vehicles would have a similar blend of impact — this technology could drive logistics further into rural America and help fill labor gaps, but a human touch will still be required.
Recent research by Uber’s Advanced Technologies Group showed the average age of U.S. truckers is 49 years old, and 55% of truckers are 45 or older. Current federal work regulations limit drivers to 400 to 500 miles daily. Autonomous trucks would have none of these issues, but implementing the technology would increase jobs another way.
Nebraska Trucking Association President Kent Grisham sees automation in the trucking industry leading to a rise in staging areas between end points, where human labor will be needed to drive a load to and from a warehouse to prepare it for the long-haul segments.
“In order for these types of trips to be feasible, the trucks need to be fully automated,” Grisham said.
Callahan said he isn’t convinced the robot overlords are out for all the warehousing jobs in the future.
“To go to the point where an entire warehouse is operating without people is maybe an ideal,” Callahan said. “But it's going to take many, many years, and they may never get to that point. Just like you never got to it in retail.”
Egan agrees that robotics will never kill all jobs — the supply-chain business is already very automated, and it employs a lot more people than it used to.
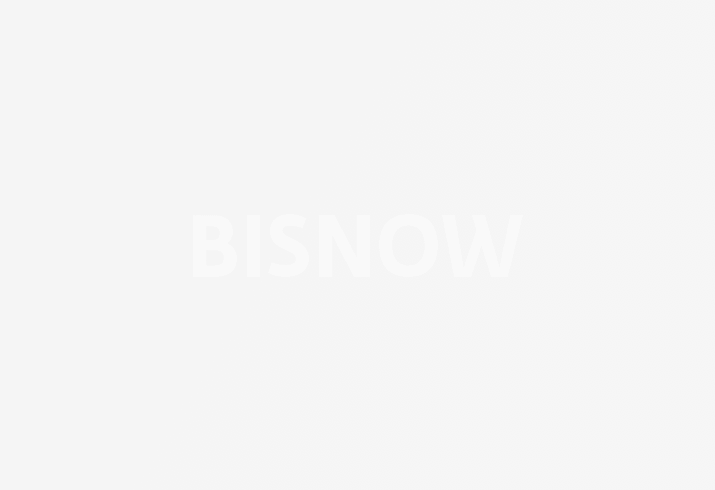
“I can certainly envision a future in which that starts to change [and] employment drops again, but people do most of these jobs better than machines,” Egan said.
From a production standpoint, it is difficult and not cost effective to completely replace workers with robots because if a product gets an update every year, the robotics need to be completely updated each year to meet the new production schedules, Cushman & Wakefield Vice President and Americas Head of Logistics and Industrial Research Jason Tolliver said.
Robots also still lack the dexterity needed and are still very expensive even though price points are starting to come down, Tolliver said.
“We’re still very far from a world where we’d have dark warehouses with no workers inside and robots filling orders and fully autonomous production lines,” Tolliver said.
Rewards Outweigh The Risks
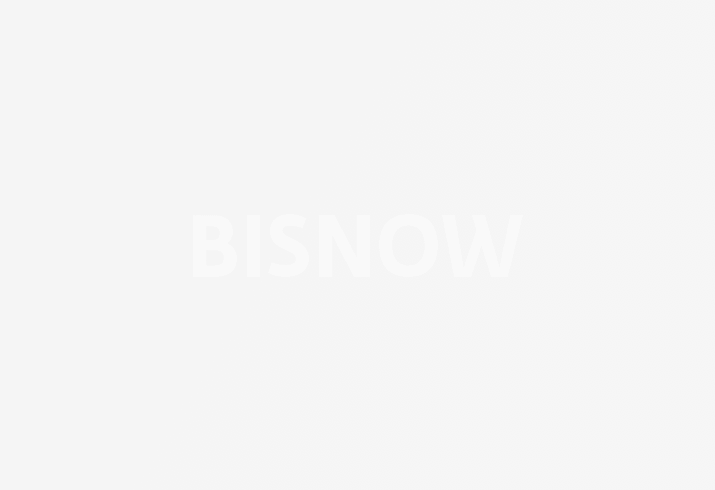
Despite the challenges of labor and risks of automation and setting up shop in rural areas, development will continue for decades to come. The South Carolina Ports Authority and national companies moving into the South find the area a boon for their operations.
Even though the industrial labor pool is tightening nationwide, Mallace said he isn’t too concerned about it drying up in South Carolina. Manufacturing facilities in the South and Southeast are now cost-competitive with countries like China and India. He said more manufacturing drives more consumption, which drives more distribution.
“The thesis is those macro factors aren’t going to change with the recession,” Mallace said. “Though there is risk, we’re bullish.”
Mallace said he also remains optimistic about Inland Port Dillon’s future. Since the newly opened port is much more of a speculative investment, it is too early to say what the future will look like, he said.
“Any big investment carries a risk with it,” Mallace said. “If we knew for sure it would be profitable and a home run, we would have done it years ago.”