The Energy in Things
Introducing our new special report on the environmental impacts of our stuff
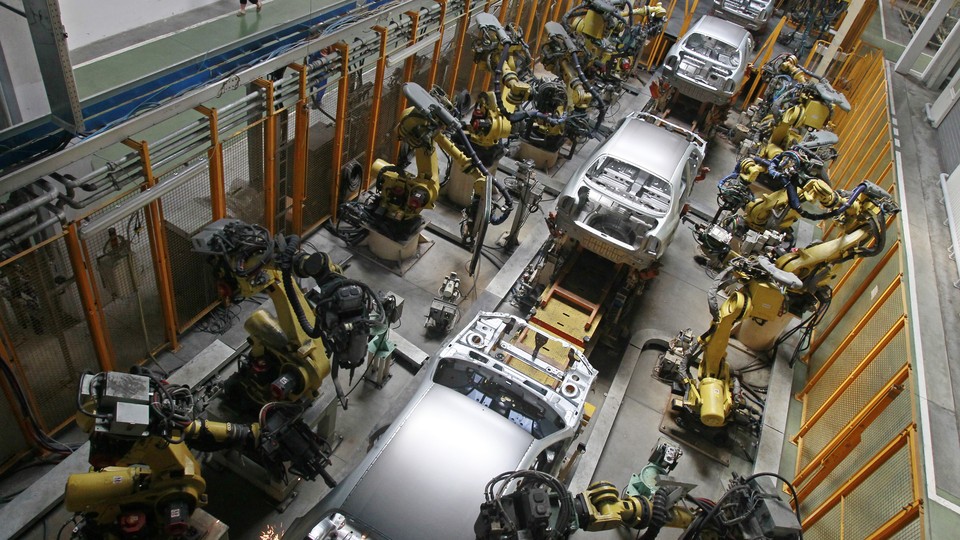
The modern cellphone user is highly attuned to energy usage. I assiduously monitor my phone's battery, tracking its decline from morning to evening, and then its return to fullness. There are even special "advanced power strips" that help people save energy while charging their devices.
But the truth is that operating a smartphone doesn't require much energy. An iPhone 6 needs just 3.8 kilowatt hours of electricity per year, according to OPower, an energy data firm.
The real energy cost to the world of an iPhone 6 is not charging its battery, though—it is creating the phone. Energy scholars call this embodied energy emergy, which is a terrible world for an interesting concept. The stuff that we own contains the ghost energy of all the production processes that went into making it.
And it takes a lot of energy to mine, refine, grow, and create materials. For a smartphone, researchers estimate that it takes roughly 1 gigajoule to create a modern smartphone. That's roughly 278 kilowatt hours, or 73 times the electricity used to charge the thing for a year.
Think about the difference of energy that's expressed here. If you're trying to reduce your personal energy consumption, does buying a smart power strip make sense? Or should you just keep your phone for an extra few weeks?
The energy embodied in the stuff of our lives represents a major—maybe the major—way that we contribute to environmental problems.
And that's why we created this special report, The New Energy Cycle. The way that things—food, phones, cars, houses—get made and then disposed of doesn't get enough attention.
When most people think about energy, they think about the gas that goes into their cars, not the steel that forms their frames. They think about the electricity that comes out of the socket, not the wood and drywall.
But there's actually some good news to be found in energy when we look outside the narrow frame of energy consumption. Almost 90 percent of steel, for example, is now recycled. That's a major victory for reducing the amount of virgin materials that need to be extracted from the earth.
The biggest obstacle to doing this work, and it's something we encountered throughout this report, is that the data isn't there. The world is complicated! And many modern products incorporate parts from all this globe. There is a field of academic study dedicated to doing this work: lifecycle analysis. It aims to provide a fair picture of the materials and energy that go into making and using things. But researchers have to make many assumptions and estimates to arrive at firm numbers. The numbers do tell us something, but the story they tell is complex.
Which is as it should be: Reducing the creation of a product like a chicken drumstick should be a complex endeavor that's hard to reduce to a few numbers. Biological processes intersect with economic methods and mechanical production. Logistical networks and cellular networks come together to produce this product we eat.
And that's what this report is all about: finding the connections between energy and the stuff we own, use, and consume.