Predicting and preventing costly breakdowns in machines
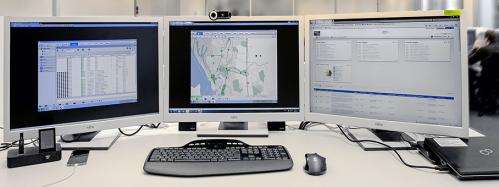
Everything's green in Duisburg. Well, almost. That's because many green dots and only one red one can be seen on a huge display that shows the city's street network. Every dot represents a traffic light. Green means everything is working perfectly; red means the opposite. Bakir Bijedic-Hoffmann, Head of the RCM Support Center in Munich, clicks on the red dot. The display tells him that one of the traffic light's red lamps has burned out. This is not a big problem, because traffic light systems generally have at least two traffic lights for each direction or two light bulbs for the red signal.
However, before the second bulb fails, a technician should replace the burned-out bulb. The computer's database reveals that an elevating platform truck will be needed to accomplish this, since the defective lamp is located in a hanging traffic light several meters above the ground. In the past, a technician would have driven to the traffic light and inspected it, then driven back to the workshop to get replacement parts or an elevating platform truck. But these days, thanks to the common Remote Service Platform (cRSP), the approximately 380 service technicians who maintain Siemens traffic lights in Germany know what to expect before they even get into a service vehicle. The cRSP is a uniform IT infrastructure consisting of computer centers and data links through which all Siemens Sectors conduct remote maintenance. Traffic computers in cities, motors in power stations, and computer tomographs in hospitals regularly transmit status data through the system to three Siemens computer centers worldwide. In return, the cRSP automatically sends software updates to some of the systems it is hooked up to. Service personnel use the status data to organize maintenance and repair of systems. In some sectors, this is even done in advance before a defect occurs.
At the Support Center in Munich, Bijedic-Hoffmann and his seven employees monitor traffic computers in 255 cities worldwide, from Abu Dhabi to Würzburg. Each year, service technicians handle around 65,000 repair and maintenance jobs in Germany alone. Control centers in Essen and Nuremberg are notified of faults either by customers or automatically by traffic computers. The centers, in turn, notify service technicians by calling them on their smartphones. In most cases, Siemens guarantees that it will have someone on the scene within two hours or will begin eliminating the fault by that time. If a service technician doesn't know how to resolve a problem, he or she calls experts in Munich, who then log into the system through the cRSP in order to find the cause of the fault. As a result, it generally doesn't take long to repair a faulty system, such as a traffic light or a traffic computer.
No Substitute for Service Contracts. Despite the advantages of remote maintenance, some cities still view it skeptically with regard to traffic management. Such cities, perhaps because of data protection concerns, prefer to do everything themselves. "People don't automatically buy remote maintenance," says Klaus Selbach, a product manager for remote maintenance services at Siemens Industry in Nuremberg. Selbach advises operators of large electric motors and transmissions. The breakdown of a motor with an output of over 250 kilowatts can have serious consequences for associated processes, and the cost of the breakdown can far exceed the cost of remote maintenance services. For example, if the drive unit of a power station's coolant pump stops working, the plant will stop generating electricity, which could cost hundreds of thousands of euros in losses each day. Nonetheless, some customers prefer to risk paying breakdown costs rather than investing in a service contract. But that can backfire. Selbach's team knows from experience that service contracts almost always pay off.
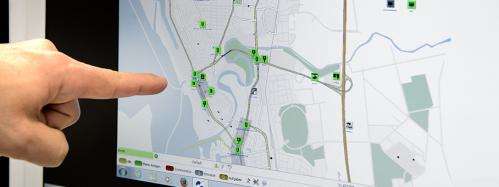
On a daily or hourly basis, condition monitoring systems transmit information on the status of motors and transmissions through the cRSP to Siemens maintenance centers. The monitoring systems report the status of motors and transmissions in power stations, mill drives at mines, cement manufacturing plants, and oil and natural gas facilities. They are equipped with temperature and vibration sensors and transmit information on torque and rpm, which reveal how much stress a powertrain is experiencing. If critical levels are exceeded, technicians can study the data in depth and even observe conditions in real time. Imminent faults, such as a worn-out bearing, can thus be discovered before the bearing falls apart in a cloud of smoke. "We've prevented several such breakdowns," says Selbach.
Keeping Medical Equipment Healthy. Predictive maintenance—the inspection and anticipatory repair of systems before they break down—uses technology developed by Siemens' Medical Engineering Group, a pioneer in the area of remote maintenance (see Pictures of the Future, Spring 2009, p. 60). Back in 1985 In England, when Siemens equipped a computer tomograph with a modem for remote-distance diagnostics, data was transmitted at only 300 bits per second. Today more than 120,000 medical devices, including magnetic resonance tomographs and ultrasound scanners, are connected to the cRSP, along with 10,000 users. The devices automatically receive software updates of up to 10 gigabytes. In 1985 it would have taken several years to transmit such a huge data packet. cRSP was developed by a network of Siemens Groups. Healthcare is the leading user, accounting for 80 percent of the data volume and functions. All other Siemens units use the same infrastructure of computer centers and transmission logs for their work, but they combine it with their own applications and business models.
Half a Million Devices by 2020. A total of 250,000 devices are connected to the cRSP—a figure that is expected to double by 2020. The Healthcare Sector alone transmits 10 terabytes of data per month through 20 million connections. Volume is rising dramatically from year to year, and is expected to reach 100 terabytes by 2020, because more and more device functions consist of software, in which faults can be easily eliminated remotely. The data gained in this way also serves as the basis for new business models, which can be developed through business analytics or by studying the correlation between medical and demographic data. "As the amount of data grows, the cRSP system will reach the limits of its scalability and costs in a few years," says Sascha Sandner, who manages the Remote Services Business at Siemens Healthcare. That's why a new technology is needed—and it's already in the pipeline.
The Siemens Healthcare, Infrastructure & Cities, and Energy Sectors have teamed up with Siemens Corporate Technology and Healthcare IT to develop a new system known as cRSP Next Generation. The new system will have a modular design, and its improved architecture will enable it to handle the substantially greater data volume that will be generated in the future. It will also have better security functions and new possibilities for connecting inexpensive equipment. New, smaller computer centers will be added, and devices will transmit data only to the center that has enough capacity at the moment. Each device contains a communications agent that decides what kind of data is to be transmitted. Sensitive information will be transmitted through expensive, highly secure lines. If required by law, the information might have to be transmitted to a computer center in the same country as the device. By contrast, less sensitive data will be transmitted inexpensively by means of cloud-based services.
Around-the-Clock Service. One of the future cRSP architecture's main aims is to enable the creation of new business models. Customers already can often choose between a basic service, which encompasses remote-distance diagnostics and software updates, and premium services with a 24/7 repair warranty. The pressure to innovate is especially high in the medical technology sector, says Sandner: "Our competitors now offer remote-distance diagnostics and even the proactive detection of imminent breakdowns."
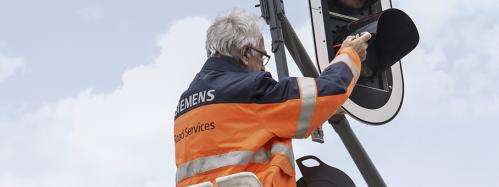
The next step is to offer interactive services such as audio/video collaboration in real time. For example, a radiologist who is having trouble with an X-ray machine could use the cRSP to establish a video connection with an application specialist at Siemens, who would remotely walk him through the steps needed to resolve the issue. On the other hand, a doctor could obtain a second opinion from a specialist at another hospital. This can already be done through cRSP today, but the next generation of the system will offer better quality even with standard equipment such as tablet computers. And it will enhance not only the company's interaction with customers, but also customers' interactions with one another.
Advanced remote maintenance could spur new applications at all Siemens sectors. For instance, experts at Building Technologies are using the cRSP infrastructure and its secure data transmission system to remotely control the facility automation systems in a hospital while their colleagues at Healthcare are using the system for the remote maintenance of computer tomographs in the same building. This approach creates synergies and wins the customer's trust. Helping customers save energy is becoming an increasingly important business model. For example, Building Technologies is using building management data to advise customers on how to save electricity and cut heating costs. Similarly, Siemens uses data from actual driving operations to give railroad engineers tips on how to operate Siemens locomotives more energy-efficiently. The savings in energy costs are split between the operator and Siemens, resulting in a win-win situation.
In 2014 a new remote maintenance era will also be ushered in at the traffic service center in Munich. In April, a new traffic light control device will be presented. It will be installed in gray cabinets at intersections, but employees will be able to override the system as though they were standing in front of the cabinets. Software updates will be automatically uploaded into the control devices. And here too, the new system will improve efficiency. "This will be especially true for emerging markets, which can't afford to employ large numbers of technicians," says department head Herbert Padinger. Cloud computing is being introduced for the system as well; ten German cities already have their traffic control activities handled by a computer located in another room in the Munich service center. The customers' transport engineers can access the system through the Internet—for example, when they plan to switch all the traffic lights to green for a major event. And they can do this from the comfort of their own homes.
Provided by Siemens