Waste360 sat down with J.M. Smucker Company’s sustainability director to discuss how the company was able to achieve its zero waste goal so quickly.
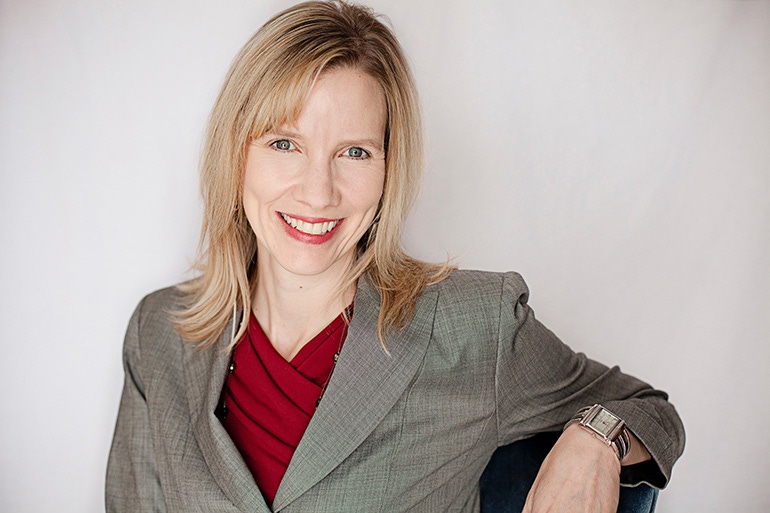
For more than 120 years, an Orrville, Ohio-based company has been manufacturing food products for both people and their pets. Best known for its brands like Smucker’s Preserves, Folgers, Jif and Milk-Bone, The J.M. Smucker Company recently announced it had achieved the company's 2020 goal of reducing 95 percent of waste from landfills a year early.
"We know that for us to truly thrive, we must take an active role in helping those associated with us thrive as well," said Mark Smucker, president and chief executive officer for The J. M. Smucker Company, in a statement. "Our Thriving Together mentality is built on a single philosophy: being a financially successful business and a responsible one are not mutually exclusive concepts."
The J.M. Smucker Company aspires to be at a 100 percent efficient state in all company facilities with respect to its environmental footprint.
“Environmental considerations have always been a key factor when we determine how to operate our facilities, develop new products and source ingredients and other materials,” says Rebecca Ott, director of sustainability for The J.M. Smucker Company. “…To achieve positive environmental impact, and as part of this commitment, we established the objective of diverting 95 percent of all waste from landfill to other sources by 2020. Reaching this goal a year early required several changes at our manufacturing facilities as well as our corporate headquarters.”
Waste360 recently sat down with Ott to discuss the company’s sustainability goals and learn how it was able to achieve its zero waste goal so quickly.
Waste360: How did the J.M. Smucker sustainability plan come about?
Rebecca Ott: Environmental stewardship has been a part of our approach for several decades, but in 2014, our leadership wanted to formalize those efforts in a meaningful, measurable way. To provide quantifiable objectives to guide our efforts, we established our 2020 environmental sustainability goals.
In addition to our landfill diversion objective, we also established the goals of reducing water usage intensity by 15 percent, which we not only achieved a year early but exceeded—reaching a 17 percent reduction in water use intensity since 2014 and GHG [greenhouse gas] emissions intensity by 10 percent. All three objectives were established based on an appraisal of where we felt we could make the most meaningful impact.
Waste360: How did the company divert 95 percent of landfill waste a year early?
Rebecca Ott: Our success in achieving the goal of diverting 95 percent of waste from landfill a year early is a testament to the dedication and hard work of our employees in each of our locations. We also require rigorous data collection and monitoring of waste reduction, reuse and diversion so that we can identify opportunities and maintain progress. We work with TRUE Zero Waste certification system to understand and implement best practices. In 2019, our Buffalo, N.Y., site achieved Gold certification from TRUE.
From our headquarters to each manufacturing facility, our employees are passionate about delivering on these objectives and doing their part to help reduce our impact on the environment. What is especially inspiring is that these strategic goals have not only impacted how our teams approach their daily work, but in many cases, they have encouraged changes in our employee’s personal lives as well. Without support from each location, this would not have been possible.
Waste360: How important were the J.M. Smucker employees in achieving your zero waste goals?
Rebecca Ott: I’d just like to reiterate the role our employees had, and continue to have, in achieving our environmental sustainability goals. At the outset, we recognized we needed to enact a cultural change and success would be dependent upon the support of every employee. I’m incredibly proud of our employees for their dedication to working toward the company’s environmental sustainability goals.
Waste360: What key learnings did you discover that other organizations can follow to achieve zero waste?
Rebecca Ott: As organizations set out to reduce waste and change the mindset among employees, we have several learnings and tips to share.
First, it’s critical to collect data on the types of waste generated within a location to understand where changes can be made. With our business, we had to examine both our manufacturing facilities and office environments and the unique waste each area presents. While the volume is more considerable in a manufacturing environment, there are opportunities to streamline processes, whereas in an office setting, each individual represents a different waste stream. We recognized these differences and engaged each audience appropriately.
Organizations need to make it as convenient and intuitive as possible for employees to recycle and compost. At our headquarters in Orrville, this meant adding new receptacles and signage that clarify the waste streams and making them available throughout our building. In the cafeteria, we now have a compost bin specifically for food waste. If employees are clear on exactly what items go where, it’s much easier for them to do the right thing.
Third-party partners can go a long way in not only reducing waste but creating a better use for it. A unique example was utilizing Grind2Energy—a biodigestion system that turns our food waste into methane to offset our power usage through a generator. In 2018, through our Grind2Energy waste, we reduced carbon emissions by 16 tCO2e [tonnes of carbon dioxide equivalent], the equivalent of 38,328 miles driven, and created 1.3 tons of beneficial fertilizer.
Evaluate the supply chain and work with suppliers to make sustainable changes. At our manufacturing facility in Buffalo, for example, we used to receive one of our liquid ingredients for our Milk-Bone brand in large corrugated cardboard totes that had a large, thick, plastic bag liner inside. These totes would frequently leak, leading to a loss of material. When the totes were empty, the plastic bag liner had to be disposed of as waste; it could not be recycled. We worked with the supplier to deliver the material in recyclable, reusable, hard plastic liquid storage totes instead. Eventually, we took it a step further and installed new storage tanks so we could receive the material in a bulk tanker truck. Now, there’s no packaging of any sort to deal with for liquid ingredients.
Find organizations that can use your waste for a good cause. Due to a product change, our manufacturing facility in Lexington, which produces our Jif peanut butter, had a surplus of plastic caps that were no longer needed. Rather than throw them away, the team at the facility identified and donated the caps to a local organization, the Kendyl and Friends Foundation, which collects plastic caps and turns them into benches for handicap accessible playgrounds.
Waste360: What cultural changes had to be made to achieve this goal?
Rebecca Ott: The focus on zero waste as part of our commitment to environmental sustainability is truly driven by employees—especially those at our facilities across the country. As such, all new employees receive training on sustainability, recycling and waste reduction during onboarding.
At each site, we have a sustainability pillar leader who facilitates implementation of sustainability strategies. At the corporate headquarters, we have sustainability ambassadors who work to encourage a sustainability mindset and to improve behaviors that lead to waste avoidance and diversion.
Waste360: What other “green” or sustainability initiatives are involved in the plan?
Rebecca Ott: As part of our sustainability goals, in 2014, we also committed to reducing water use intensity by 15 percent and GHG emissions intensity by 10 percent by 2020. We are ahead of schedule in achieving our water reduction goal, already reducing our water use by 17 percent. We are also well on our way to achieving the 10 percent GHG emissions goal and are currently at 6 percent reduction.
As part of our efforts to reduce GHG emissions, we entered a long-term virtual power purchase agreement with Lincoln Clean Energy, LLC to help finance the creation of a utility-scale wind project called the Plum Creek Wind Farm in Wayne County, Neb. A portion of the renewable energy produced there is expected to address approximately 50 percent of our total electricity use starting in 2020. This agreement will not only reduce our carbon footprint but will also allow us to make a lasting contribution to our nation's renewable energy capacity.
About the Author(s)
You May Also Like